Case Study 4 : Auto Parts Manufacturer
Auto Parts Manufacturer Chooses Asprova For Scheduling Speed
Reduces Setup Time and Inventory in Two Months
-F-Tech Inc. –
F-Tech Inc. primarily manufactures suspensions and rear axle beams for automobiles. Before introducing Asprova, they made schedules relying on their intuition and experience based on required quantities calculated by the mainframe computer. Frequent changes in orders, however, put a heavy load on scheduling managers and caused inconsistency between material ordering and scheduling. To resolve this situation, they have introduced Asprova, a popular high-speed scheduling system, and DISP, a production management module. The introduction of these systems has reduced not only the load on scheduling managers but also inventory in a short period of two months after actual operation began.
Problems Prior to Introduction
- Heavy workload for scheduling managers trying to keep up with frequent order changes through manual scheduling methods
- Excessive inventory hoarded to avoid late delivery and confused production in the face of frequent schedule changes
- Excessive raw material inventory and hand-writing of material orders due to inconsistency between material ordering and scheduling
Reasons for Introducing Asprova
- Asprova’s scheduling speed
- Asprova’s diverse standard features
- Asprova’s fast scheduling speed
Benefits of Introduction
- Cut time required to make a schedule down to a couple of hours, reducing the workload of the scheduling managers.
- Improved accuracy of scheduling, reducing setup time, lead time, and inventory.
- Enabled source data for material orders to be sent automatically to the mainframe computer, preventing material shortages.
Heavy Load on Scheduling Managers
The mainframe computer in F-Tech receives order data once a month covering a period of three months and receives data on order changes daily. Before introducing Asprova, however, material requirements were generated only once a week on the mainframe because it took too much time and they had no way to take into account the load on the line. As a result, scheduling managers had to make daily schedules based on their own intuition and experience, manually transcribing order changes and taking into account the inventory and load on the line. Despite their effort, it was very difficult to handle the great number of order changes, and careless mistakes would inevitably occur. Since accurate scheduling was quite difficult, they were forced to change schedules frequently, taking on an excessive workload. As Katsumi Arima of the Production Management Department of the Production Division says, “The whole day would be taken up just adjusting the schedule.” These frequent changes in the schedule would in turn force the factory floor to keep extra inventory of intermediate parts to prevent late delivery and confusion in production. Also, the manually-drafted production plans and material orders did not match because materials were ordered based on the data in the mainframe, which did not reflect the manual changes. Again, they were forced to order materials manually to keep extra inventory so that the production line could go on running.
“The first thing we needed,” said Toru Okutomi, Manager of the Production Management Department, Production Division, “was to reduce the man-hours required for scheduling.” Thus, among various objectives, they recognized the most important one to be the reduction in the load on scheduling managers. After comparing several modules, they were most impressed with the high-speed scheduling and the standard features of Asprova. In terms of scheduling speed, in particular, Arima said that Asprova was by far the fastest.
Since, however, as Okutomi explains, “we needed capabilities that would enable peripheral connections besides scheduling,” they decided to introduce Asprova together with DISP, a production management module from NEC Techno-Service, an Asprova distributor.
Results Within Two Months of Operation
When it came time to install Asprova and DISP, F-Tech took charge of preparing the necessary data and determining the system specifications, while NEC Techno-Service took charge of most of the system development. “Determining the specs was not an easy job,” Arima said. “Also, we got a lot of errors because the mainframe’s configuration charts didn’t include the process codes, and correcting these errors took a lot of time.” Since he had to do regular work as well, he says, it took time to get ready for the test run.
Now, after the installation of Asprova, the schedule can be created in a couple of hours, reducing the load on the scheduling manager, which was the initial objective. Asprova has also enabled accurate scheduling making full use of the precise data prepared at installation. As a result, the factory not only produces items as scheduled but has also been able to reduce setup time, lead time, and inventory. They can now order materials by sending source data directly to the mainframe so that sufficient materials can be kept all the time. Although only two months have passed since they started operating Asprova, they are already enjoying various benefits. “I think we will have further good effects as time passes,” says Arima.
In the future, F-Tech is planning to deploy PC terminals at each process to enter the results data that is now written on daily reports, and to create a system to confirm schedules using the Asprova Scheduling Monitor, thus more efficiently utilizing Asprova and DISP.
Figure 1: System Configuration
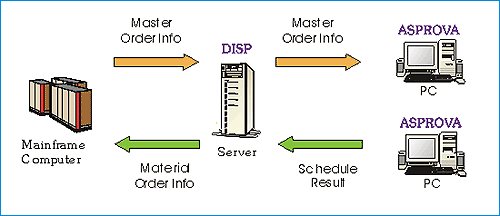
Master order information is sent from the mainframe, and scheduling is performed by two Asprovas linked with DISP. The resulting schedule is then used for generating work instructions, and part of the data is returned to the mainframe to be used for issuing material orders.
Figure 2: Gantt chart created through scheduling with Asprova

Changes and additions are identified by color or by fixing the associated jobs in place.
Figure 3: One of the screens from DISP

These screens are customized to the user’s needs
Data Volume | |
---|---|
Finished products | 600 |
Total items | 5,150 |
Resources | 58 |
Processes | 5 |
Scheduling period | 3 months |
Scheduling cycle | constantly |
Lots in scheduling period | about 45,000 |
Jobs in scheduling period | about 150,000 |
F-Tech Inc.
Since its establishment, F-Tech Inc. has manufactured auto parts such as suspension assemblies, sub frame comp., and rear axle beams. The company has numerous patents and utility model rights regarding auto parts such as a pedal leg-power reducer and a foot-operated parking brake.
Left to right: |
Chooses Asprova for scheduling speed Reduces setup time and inventory in two months Read More… |
![]() |